— (B)革新的生産・製造技術の研究開発 —
超3D造形技術プラットフォームの開発と高付加価値製品の創出
Development of super 3D fabrication platform and production of high value-added products 光造形3Dプリンタの精度と速度向上と、多様な材料への対応拡大に取り組む
詳細・最新情報はテーマ先ホームページから
http://super-3dfab.ynu.ac.jp/
- 研究実施機関(再委託先、共同実施先含む)
- 横浜国立大学、(地独)神奈川県立産業技術総合研究所
背景
光造形法は、高精度に透明な3D物体を作製できるため、工業製品の試作や機能検証に幅広く用いられています。また、近年ではより高精度なマイクロ光造形法の研究開発も活発化しています(図1)。一方、実用製品の作製には現状、以下のような課題があります。
- マイクロ・ナノ造形の描画線幅の拡張と造形速度の向上
加工線幅・造形速度がスポットサイズによって制限されてしまう課題。
- 積層段差による加工精度の低減
3Dプリンタの共通課題である積層方向に生じる段差。
- 適用材料の制限
光硬化性樹脂のみ利用可能であること。
本テーマでは、こうした課題の解決に取り組んでいます。
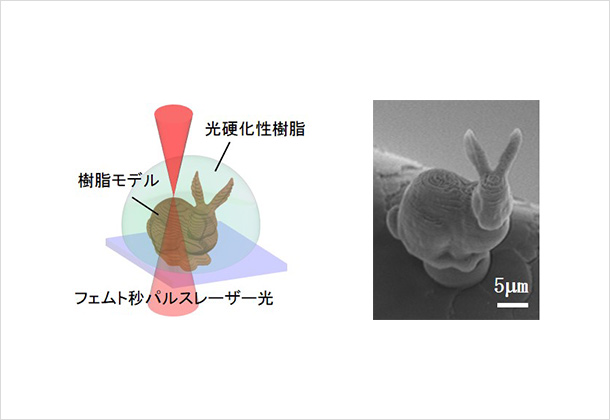
目標
- 加工線幅の自在制御によるシームレス3D造形(線幅:50nm?100μm)
- 3D空洞化モデルによる造形時間の短縮(1/10以下)
- マルチスケール全方位型造形による高精度な3D造形の実現
- 鋳型技術による多様なセラミックス機能素子の創製(図2)
- 生体適合ゲルを用いた人工臓器の開発(cmサイズ)
- 超3D造形技術プラットフォームによるオープンイノベーションの実践
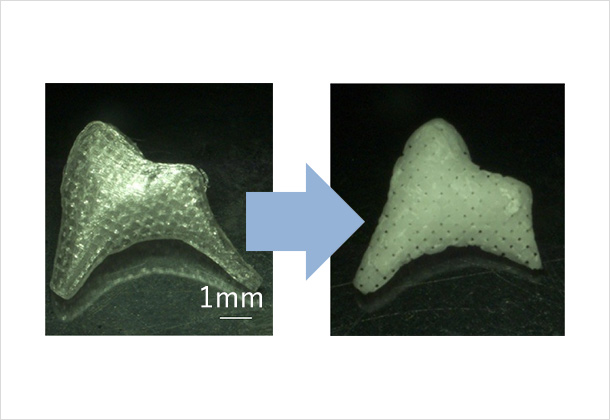
- 波及効果
- MEMS、ウエアラブルデバイス、フォトニクス、先端医療などへの応用に期待
実施内容
- マイクロ・ナノ造形の描画線幅の拡張と造形速度の向上
空間光変調による集光スポットの自在制御
従来法で困難な加工線幅の補完
空洞化CADモデルによる高効率造形 - 積層段差による加工精度低下の改善(図3)
あらゆる方向から積層造形が可能な全方位型造形システムの提案・開発
- 適用材料の拡大
鋳型技術によりセラミックスやゲルなど多様な材料で3D機能素子を作製
- オープンイノベーションへの取組み
青色レーザーを用いた1μmの加工分解能を持つ装置を実現。神奈川県産業技術センターに設置し、オープンイベーションの取組みを推進。
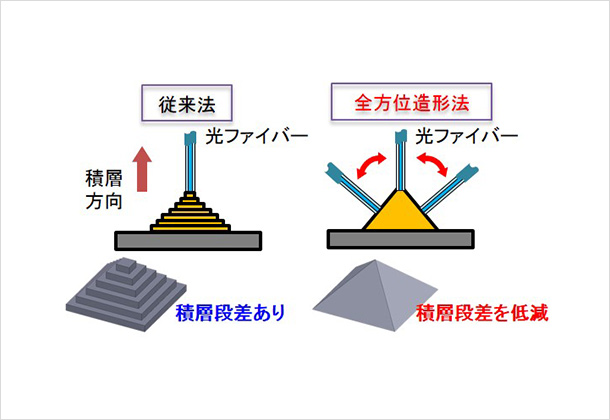
研究成果
- ツール/技術
- 活用の場
- イノベーションスタイル
詳細・最新情報はテーマ先ホームページから
http://super-3dfab.ynu.ac.jp/